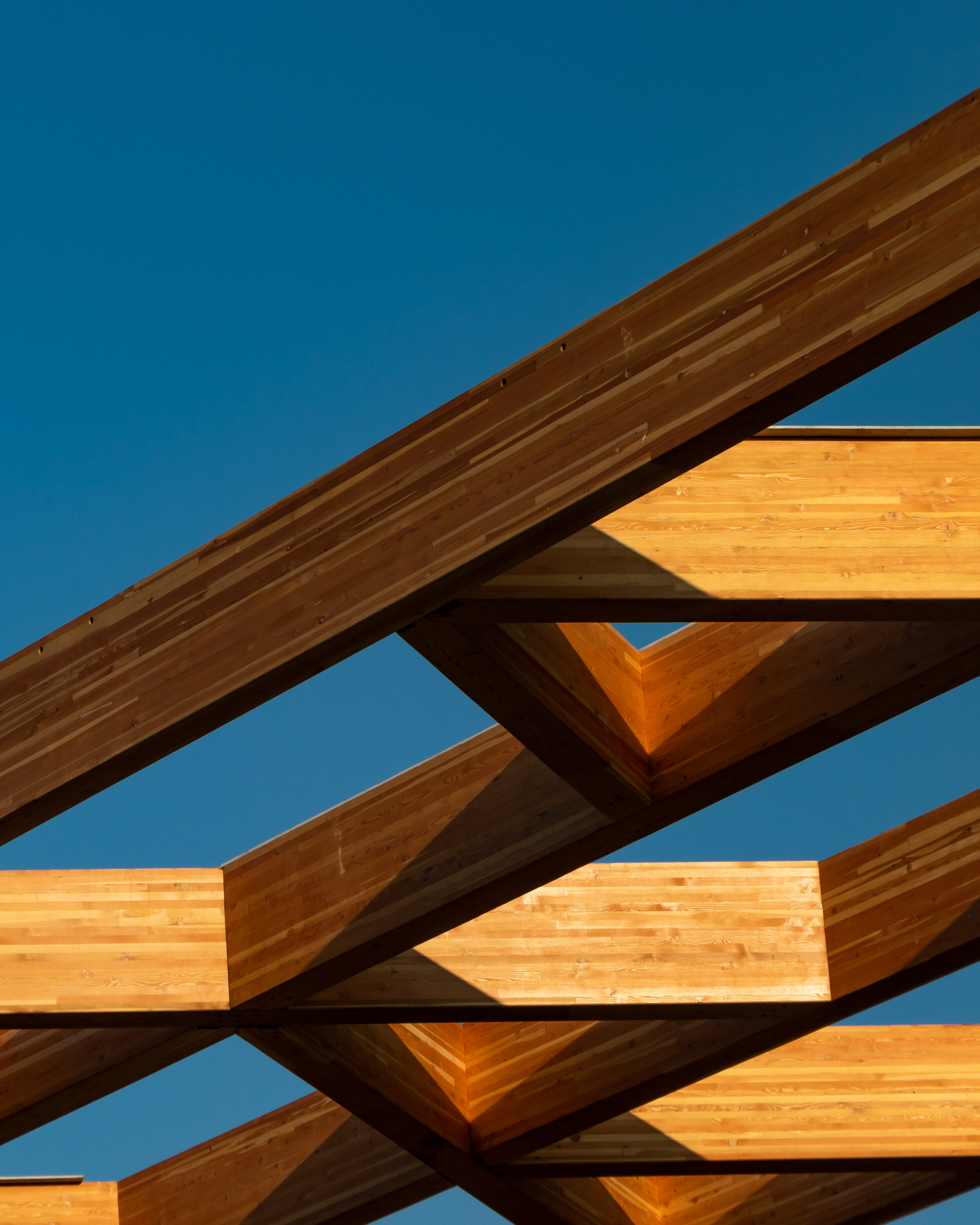
ISO 9001:2015 Quality Management System Certification
Every organisation strives to operate efficiently, in an effective manner so that it can deliver the best results. No matter the industry, organisations have an obligation to deliver their products and services in a timely manner and to the same standard every time. To achieve this, your organisation needs an effective Quality Management System that is focused on continual improvement and client satisfaction, and is effective in communicating these expectations to your workforce.
Like other International Management System Standards, ISO 9001 is based on the well known and widely utilised Plan-Do-Check-Act (PDCA) process. The PDCA process is essential to Quality Management, as it facilitates continual improvement by merely existing.
Used by companies worldwide to facilitate continual improvement, the PDCA is a circular model - there is no end to the process - hence the term ‘continual improvement’. It can be implemented to the overarching Management System and to each of its individual items and is facilitated in the following manner within ISO 9001:
PLAN: the organisation identifies their current capacity and analyses its outcomes, then identifies ways in which these can be improved. A plan is created.
DO: implement processes, allocate resources and communicate objectives as per plan, ensuring training and awareness is provided.
CHECK: monitor and review effectiveness of plan via comparison to set quality management objectives.
ACT: take actions to ensure continual improvement of intended quality outcomes.
What does ISO Certification under ISO 9001 mean for my organisation?
ISO Certification under ISO 9001 means that you’ll be one of over one million companies worldwide operating efficiently under an international Quality Management Framework. ISO 9001 requires a disciplined management approach, and can benefit your organisation in many aspects including:
Providing employees with a clearer understanding of the importance of their role within the success of the organisation, leading to improved morale.
Recognition of your company’s commitment to Quality Assurance, not only nationally but world-wide.
A methodical decision making process, focusing on factual experience.
Improved productivity and efficiency, leading to increased profitability.
The development of beneficial supplier relations.
Increased consistency through the documentation and formalisation of all processes.
Ensuring customers receive consistent service, leading to increased satisfaction.